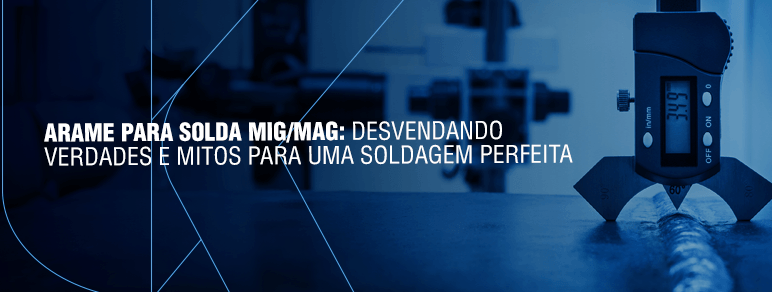
A soldagem MIG/MAG é amplamente utilizada na indústria metalúrgica devido à sua versatilidade e eficiência. No entanto, o sucesso desse processo depende de diversos fatores, sendo o arame de solda um dos mais críticos.
Neste artigo, vamos explorar a importância do arame nesse processo, como escolher o arame certo, os benefícios de usar arame de alta qualidade e os erros comuns ao utilizá-lo. E, mais importante, vamos desmistificar algumas crenças populares sobre a utilização do arame.
O que é solda MIG/MAG?
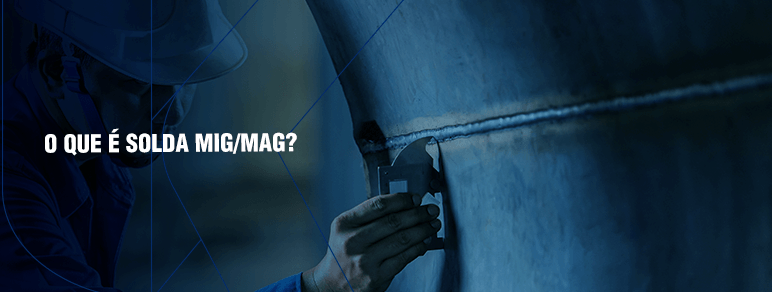
MIG (Metal Inert Gas) e MAG (Metal Active Gas) são dois processos de soldagem a arco que utilizam um arame de eletrodo contínuo como material de adição. A principal diferença entre os dois é o tipo de gás utilizado: o processo MIG usa um gás inerte, como o argônio, enquanto o processo MAG emprega um gás ativo, como o dióxido de carbono (CO2), ou uma mistura de gases.
Quer saber mais sobre como eles funcionam? Leia este outro artigo aqui!
A importância do arame na soldagem MIG/MAG
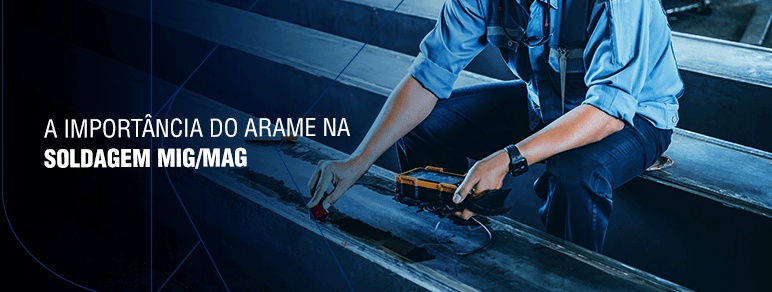
O arame utilizado na soldagem MIG/MAG é fundamental para a qualidade do cordão de solda. Ele é responsável por fornecer o material de adição que se funde com as peças a serem soldadas, e suas características influenciam diretamente a resistência, durabilidade e acabamento da solda. Portanto, escolher o arame correto para cada aplicação é essencial para garantir um resultado final satisfatório!
Alguns critérios básicos para ajudar no processo de escolha do arame:
Tipo de material a ser soldado: o arame deve ser compatível com o material da peça. Por exemplo, para soldar aço-carbono, um arame de aço-carbono é ideal, enquanto para alumínio, deve-se utilizar um arame de alumínio.
Espessura do material: materiais mais espessos exigem arames de maior diâmetro para garantir uma penetração adequada da solda.
Tipo de gás utilizado: certos arames são otimizados para funcionar com determinados gases de proteção. A escolha do arame deve considerar o tipo de gás a ser utilizado, seja ele inerte ou ativo.
Posição de soldagem: alguns arames são projetados para soldagem em todas as posições, enquanto outros podem ser específicos para soldagem em posições horizontais ou verticais.
Cada aplicação de soldagem possui requisitos específicos, e a escolha do arame deve ser feita com base nesses requisitos. Usar o arame errado pode comprometer a integridade estrutural da solda, além de aumentar os custos de produção devido à necessidade de correções e retrabalhos.
Os benefícios de um arame de alta qualidade
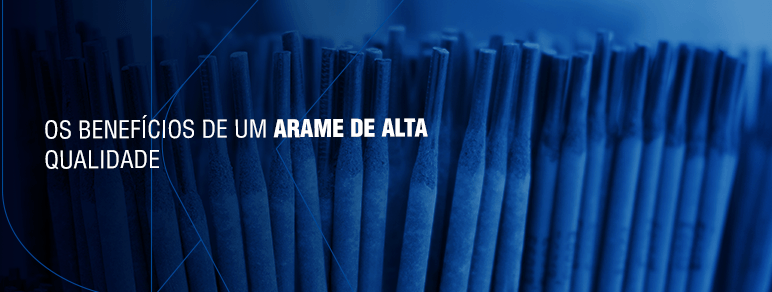
A qualidade do arame utilizado na soldagem MIG/MAG não deve ser subestimada. Um arame de baixa qualidade pode resultar em soldas fracas, porosas e com acabamento irregular. Além disso, arames inferiores podem gerar maior quantidade de respingos, aumentando o tempo de limpeza e reduzindo a eficiência do processo.
Arames de qualidade superior apresentam maior resistência mecânica, resultando em soldas mais fortes e duráveis, reduzindo a necessidade de retrabalhos. A qualidade do arame também influencia diretamente na aparência do cordão de solda, garantindo um acabamento mais limpo e uniforme.
Arames de alta qualidade produzem menos respingos, o que reduz o tempo de limpeza pós-soldagem, e proporcionam uma soldagem mais estável, com menor risco de falhas ou defeitos.
Os erros mais comuns ao utilizar arame para solda MIG/MAG
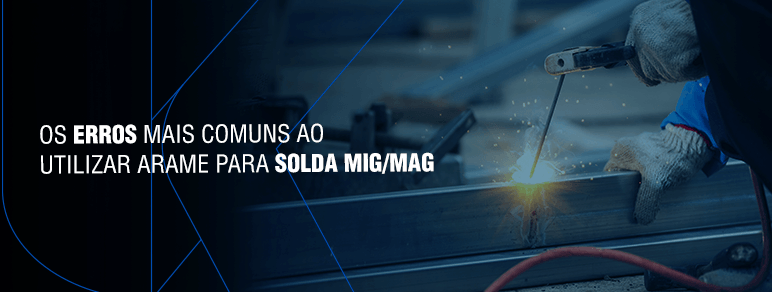
Mesmo com arames de alta qualidade, alguns erros podem comprometer o processo de soldagem.
Aqui estão os erros mais comuns e como evitá-los:
Escolha errada do diâmetro do arame: usar um diâmetro inadequado para a espessura do material pode resultar em penetração insuficiente ou queima excessiva. Consulte sempre as especificações técnicas para escolher o diâmetro correto.
Incompatibilidade do arame com o gás de proteção: certifique-se de que o arame é compatível com o gás utilizado para evitar problemas na soldagem.
Velocidade de alimentação inadequada: ajuste a velocidade de alimentação do arame conforme o material e o tipo de solda desejado. Velocidades muito altas ou muito baixas podem causar defeitos no cordão de solda.
A manutenção e o armazenamento adequados do arame também são importantes para preservar sua qualidade e desempenho. Algumas dicas importantes incluem o armazenamento em local seco, protegendo-o da umidade para evitar a corrosão, além de deixá-lo armazenado em sua embalagem original até o momento do uso, para evitar contaminação por poeira ou outros materiais.
Qualquer arame serve? Já vimos que não!

Uma crença popular é que qualquer arame pode ser utilizado na soldagem MIG/MAG, mas isso não poderia estar mais longe da verdade! Como vimos, a escolha do arame correto é fundamental para garantir a qualidade da solda e a integridade da peça final. Usar um arame inadequado pode resultar em soldas defeituosas, com menor resistência e maior suscetibilidade a falhas.
Na Kiferro, oferecemos arames para solda MIG/MAG de alta qualidade, projetados para atender às mais rigorosas exigências da indústria. Nossos arames são fabricados com materiais de primeira linha e submetidos a rigorosos testes de qualidade para garantir um desempenho superior em cada aplicação. Ao escolher os arames da Kiferro, você pode ter certeza de que está investindo em qualidade, durabilidade e eficiência para suas operações de soldagem!