O processo de solda MIG/MAG é um dos tipos mais conhecidos de soldagem, utilizado desde sua introdução, na década de 20, e viabilizado comercialmente a partir de 1948. A solda consiste em um processo constante de alimentação de um arame de solda consumível, de polaridade positiva, direcionado para uma peça metálica, de polaridade negativa — tudo sob uma atmosfera de proteção gasosa. Quando esse arame entra em contato com o metal, o circuito é fechado, permitindo a circulação de corrente elétrica entre os dois polos, positivo e negativo, gerando a chamada “poça de fusão”. Esse processo ficou caracterizado no mercado como MIG/MAG, mas cada sigla tem seu significado. Você sabe a diferença?
A SOLDA MIG
MIG é a sigla para Metal Inert Gas — quando o gás de proteção utilizado na fusão é inerte, como o argônio, por exemplo. O processo de solda MIG pode ser utilizado em aço inoxidável, aço normal, alumínio, cobre, magnésio, chapas de metal e placas estruturais, podendo operar por grandes períodos de tempo. Em função de ser uma solda de rápida execução, é a melhor opção para indústrias com alta taxa de produção, oferecendo uma baixa taxa de distorção das peças. Como o gás utilizado não é inflamável, é o próprio arame de solda que proporciona a queima, tendo em seu interior materiais que também geram uma atmosfera de proteção.
A SOLDA MAG
Ao contrário da solda MIG, a solda MAG — Metal Active Gas — utiliza gás ativo como proteção. Esse gás, geralmente o CO2 puro, participa ativamente das alterações metalúrgicas da solda ou da poça de fusão. O processo MAG também permite a mistura de gases (CO2 + argônio) para ser utilizado na soldagem de aços inoxidáveis, por exemplo. Utilizada em materiais mais ferrosos, a solda MAG contempla trabalhos de toda a área industrial.
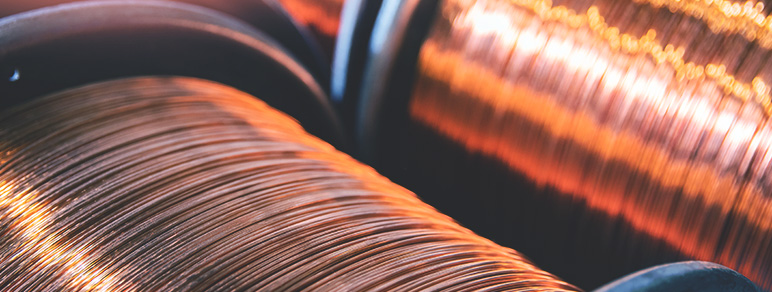
A IMPORTÂNCIA DO ARAME DE SOLDA MIG/MAG
A escolha correta do arame de solda depende sempre do material base a ser soldado, e na maioria dos casos se utiliza o arame com composição mais semelhante possível: se for soldar cobre, o arame terá composição de cobre, por exemplo.
O arame de solda é essencial para a solda MIG/MAG, já que para a poça de fusão acontecer ele deve ser alimentado continuamente, com a velocidade controlada por equipamentos de solda, enquanto o fluxo de gás envolve a região de solda e protege o material da contaminação dos agentes da atmosfera.
Os primeiros tipos de arame introduzidos no mercado para solda MIG/MAG foram os arames sólidos — e continuam sendo utilizados. Inicialmente feitos de alumínio e aço carbono, hoje acompanham a evolução das ligas de materiais que foram surgindo com a evolução da metalurgia. Mais tarde, surgiram os arames tubulares, que proporcionam a queima e fazem a função de proteção do arco elétrico em relação à atmosfera.
Outra variação desses arames de solda são os arames de alma metálica, que também são tubulares. Em seu interior, são compostos por um pó metálico que serve como material de adição durante a solda. Suas grandes vantagens em relação aos arames sólidos são a alta deposição do metal e a alta velocidade de soldagem.
COMO USAR O ARAME NA MÁQUINA DE SOLDA MIG/MAG?
O primeiro passo é encaixar corretamente o carretel na máquina. Em seguida, é preciso deixar a ponta do arame reta, para encaixar em uma guia de saída e passar por uma roldana ranhurada, que está direcionada para a guia de entrada. A roldana deve ser da mesma medida que o arame. Depois, a medida de pressão deve ser ajustada conforme a alimentação do arame, evitando assim que ele se dobre durante a soldagem.
Os arames para solda MIG/MAG normalmente possuem um diâmetro que varia de 0.6 a 1.6 mm. A definição do melhor diâmetro de arame depende da aplicação ou tipo de solda a ser executada. Outros fatores que ajudam na definição da escolha certa do diâmetro do arame:
Espessura da chapa a ser soldada: chapas menores do que 6 mm de espessura geralmente utilizam arames de 0.8 a 1.0 mm de diâmetro.
Potência do equipamento de solda: uma fonte de energia de 200 amperes não deve utilizar arame de 1.2 mm, recomendando-se diâmetros de 0.6 a 1.0 mm. Para trabalhos que necessitem de alto fator de trabalho, deve-se optar por fontes de energia acima de 300 amperes.
Posição de solda: soldas fora de posição normalmente pedem por diâmetros de 0.9 a 1.0 mm, mas também considerando a espessura da chapa.
Tipo de junta e de transferência metálica: em soldas por curto-circuito e em juntas que apresentam aberturas excessivas é recomendado o diâmetro de até 1.2 mm, para possibilitar bom acabamento.
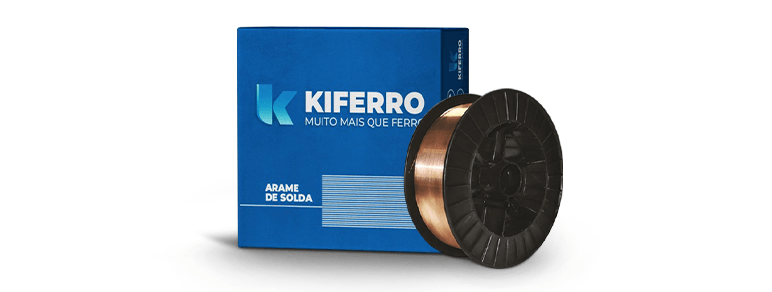
ARAME DE SOLDA KIFERRO
Disponível em diâmetros de 1.0 e 1.2 mm, a Kiferro disponibiliza seu arame de solda ER70S-6 em carretéis de 15 kg. Dinâmico, permite a soldagem em todas as posições e pode ser aplicado com gás de produção puro ou com misturas, proporcionando excelente desempenho tanto em aplicações leves quanto pesadas.
A excelência do nosso arame vem do respeito às normas e especificações exigidas e comprovadas em testes de qualidade de grandes laboratórios. Desde 2008, o arame de solda MIG/MAG da Kiferro é referência de qualidade e alta performance, conquistando os mercados mais exigentes — aprovado como o principal insumo na linha de produção de conceituadas empresas, dos mais variados segmentos.
Com a Kiferro, você pode adquirir arames de solda e muito mais! Temos um amplo mix de produtos, que atende suas necessidades. Entre em contato e faça um orçamento!